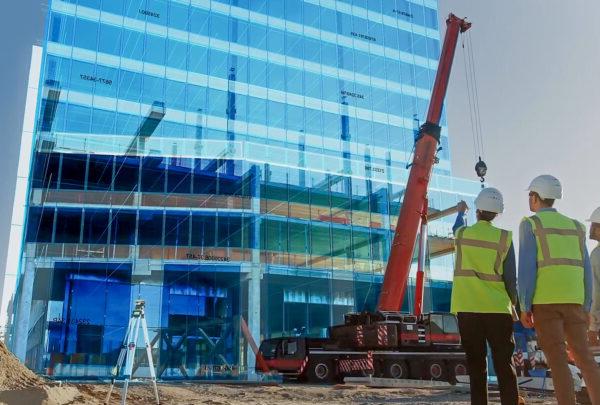
We provide fully integrated facility solutions that ensure the execution of capital projects across markets, offering local presence and global reach to the private and public sectors.
With broad-based expertise across disciplines, we are an unparalleled source for performance-driven facilities built to deliver, from concept to ribbon-cutting.
With a broad range of in-house engineering expertise, we can optimize your current operations or take your new project from concept to completion, providing unrivaled service and results.
澳门足彩app is a global network of experts providing integrated design, engineering, construction and professional services to clients and communities.
Home / News & Insights / Don’t Hire a System Integrator Until You Have the Right Answers to These Critical Questions
Integrating a controls systems in a process and/or packaging line is a complex undertaking. Many companies claim the ability to perform it, but far fewer can claim that they do it well.
If you are in the market to build a new line or upgrade an existing one by integrating new equipment centers or enhanced automation and controls, asking the right questions of your prospective integrator and getting the right answers is critical to optimal performance and maximum return on investment.
So here is a starter set of questions and the reasons that each is important.
If not, they will need a good functional description or a description of operation to write the code.
This can get into a long-term licensing or support contracts for future upgrades if proprietary code is used. Other firms may not be able to support the system in the future.
If the code is proprietary, only the integrator will be able to provide support in the future.
The programmer has more ownership in the code they write if they go onsite to commission the system.
Some integrators will only provide you with the system they are selling and not what you need.
Not all integrators want to deviate from their standard systems and incorporate client standards.
Some integrators will write ActiveX and other code that is required for the system. This can be an issue when you want to upgrade the system in the future.
Some integrators will sacrifice system performance for flashy graphics and look and feel.
Not all integrators understand the end products of their systems or the requirements to produce them.
Most software and hardware manufacturers will provide guidelines or best practices. If the system is not designed within these guidelines, manufacturer support can be an issue.
Not all integrators understand the codes and regulations of the agencies that oversee a product such as 3-A, Project Management Office (PMO), Food Safety Modernization Act (FSMA), etc.
You want a system that your maintenance team can support to prevent frequent calls to the integrator for service and support.
Onsite and remote support are sometimes needed to work through an issue. You want to make sure you have someone to contact in a time of need.
You want a system your team can maintain and run when all the contractors have left the site. Training is one way to make sure your team is ready.
Not all integrators listen to the client. You will get the system they have, but you may not want.
In today’s environment, systems must be able to track product genealogy and usage.
You want to be able to protect system operations based on the needs of your facility.
With more than 300 engineers specializing in process, packaging and material handling, 澳门足彩app and its subsidiary Seiberling provide the collaborative and holistic experience that few if any competitors can. To learn more about automation capabilities, contact Jeff Pearse, Design Director – Consumer Packaged Goods Process Engineering at jeff.pearse@hrfjk.com.
澳门足彩app delivers $2± billion annually in Architecture, Engineering, Construction (AEC) and Consulting solutions to assure certainty of outcome for complex capital projects worldwide. 澳门足彩app is a global, fully integrated, single-source design-build and EPC firm with over 2,400 highly specialized, in-house design, construction and administrative professionals across industrial and commercial markets. With 25+ office locations around the globe, 澳门足彩app is a trusted partner for global and emerging clients.
Steam-in-Place (SIP) Operations, often used in the food and life sciences industries, use the thermal energy of condensing...
Packaging requires a wide array of machinery and systems, usually made by different original equipment manufacturers...
Clean-in-place (CIP) and steam-in-place (SIP) are essential pieces of the cleaning puzzle for manufacturing facilities,...
Simulation provides companies with unparalleled insight into operations and a unique competitive advantage in the marketplace....
At 澳门足彩app, we’re frequently asked about accumulation on packaging lines. How much is right for a line? Which type of accumulator...
Speed to the market is considered one of the advantages of integrated project delivery, but what 澳门足彩app’s project team...
Engineers at a large consumer products company believe they have an intractable code problem with a laner. Unbalanced...
Consumers’ habits have changed drastically in recent years, steered by the pandemic, nutritional trends, environmental...
Since she became the director of 澳门足彩app’s packaging operations and its Atlanta office in late 2016, Bela Jacobson’s career...
A flat start-up curve can ruin your game. Demand goes unmet. Startup costs rise. And despite your best efforts to reach capacity,...
No one knew quite what to expect at Pack Expo — the mega trade show billed as the world’s most comprehensive packing...
This year’s Pack Expo, scheduled for September 27-29 amid the bright lights of Las Vegas, Nevada, will highlight the manufacturing...
Summer internships are, by definition, entry-level positions. But for Luke Mason, participating in 澳门足彩app’s Summer...
In addition to its accustomed practice of developing Project Engineers organically, 澳门足彩app currently has immediate...
Construction safety training, such as fall protection and proper protocols for excavation and ladder safety, is a common...
Production line anomalies that adversely affect plant operations are frustrating. It’s worse when the problem can’t...
I have always been fascinated by the design aspect of product packaging, but I have not really considered the mechanics...
Automation and controls bring packaging lines to life with as much — or little — human assistance as desired for consumer...
For more than 50 years, 澳门足彩app has served as a leader in the architecture, engineering and construction industry, driven...
From filling to capping to labeling to case packing — and every step in between — 澳门足彩app’s packaging systems designers...
For Emily Moseley, engineering isn’t only a job. Inspired by a former teacher and mentor, Moseley discovered her interest...
Growing up, 澳门足彩app Project Superintendent Terry DeMauro enjoyed repairing the mechanical equipment on his family’s...
As a construction manager in 澳门足彩app’s Mexico City office, Waldo Salado delivers solutions. Salado helps to lead projects...
Have you been challenged to install a packaging line quickly? This is becoming a frequent occurrence as companies strive...
A client came to us with a familiar problem: Their bottling line was fraught with multiple efficiency and quality problems....
Inventory management is the process of managing the flow of goods through a system. Although deciding where and when to...
From brunches to baseball games, the popularity growth in wine consumption, particularly among younger generations,...
A clean-in-place (CIP) system is among the largest users of consumables at a hygienic processing plant. Presented here...
Every large capital project will have unplanned and unexpected costs because it’s simply impossible to foresee and plan...
This paper will succinctly define OEE, provide examples of its contributing components, and share best practices for...
Experience shows that project success directly correlates to the team chosen to accomplish the project goals. Research...
Designing a packaging line can be a complex task. In order to describe the process to our clients, our team has found it helpful...
A great football team required great talent, but talent alone does not guarantee success. Players need to be trained to...
The ability to guide clients with data-driven decisions that maximize their return on investment is critical in any manufacturing...
With any processing plant, uncertainty presents unique challenges when managing capacity for growth. Will adding or...
Are you looking for ways to maximize the return on investment in your facility? Most manufacturers are. With this client...
How do you translate process design knowledge to other disciplines in a timely fashion? Our process-engineering team...
Seemingly, we’re all on the go. People constantly find ways to do more with the same amount of time. Some people join a teleconference...
What if shifts in consumer demand drive your organization to manufacture a new trending product? What if you need to build...
Whether you are a food, beverage, fine chemical or pharmaceutical manufacturer, there are questions that are common to...
Are you tired of traffic? Do you want the answers to solve all of your traffic woes? Unless everyone in your city reads this...
Are your process systems sterile? Steam-in-Place (SIP) Operations are used in the food and biotechnology industries,...
The beam simply does its job. Principals dictated by the laws of physics authenticate the beam as a yeoman of industrial...
Stop reading this blog — not forever, just for a few seconds. Look away from your screen and take in everything around you.�...
Simulation software that uses a physics engine can exponentially increase the advantages of manufacturing system design,...
While product-line simulation helps to address potential issues during the design phase, product-line emulation extends...
The race to market in consumer packaged goods is teeming with obstacles along the design, testing, manufacturing and distribution...
111 Riverside Avenue
Jacksonville, FL 32202
© 2024 澳门足彩app. All rights reserved.
We collect basic analytics to improve your experience. No personal data is stored. By continuing to use this site, you acknowledge this. For more details, see our Privacy Policy.